Autonomous Off-Highway Vehicles: Ergonomics and Access Control in the IoT Era
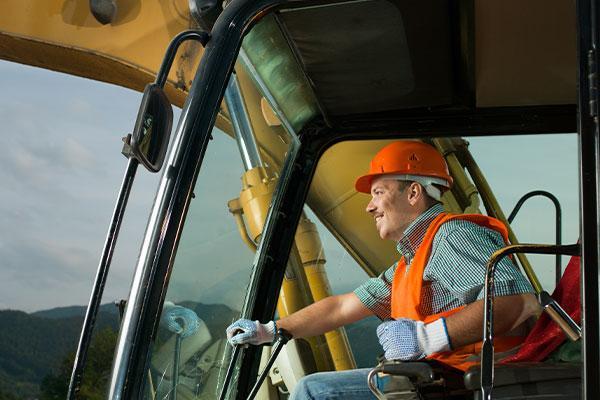
In the off-highway vehicle industry sector, there are two critical technology trends that are rapidly converging: autonomous and semi-autonomous equipment, and the progression of the Internet of Things (IoT) – a network of intelligent devices connected to the Internet to provide remote control and monitoring of the connected devices.
The IoT encompasses more than factory automation, infrastructure and logistics systems: Smart technology can comprise monitors, actuators, controllers and other devices being woven into a broad array of hard-working off-highway vehicles and equipment. Data generated from connected vehicles becomes readily available and useful, providing off-highway equipment owners and operators with the ability to manage and utilize these “smart vehicles” in a more sophisticated way.
Simultaneously, there is growing use of autonomous and semi-autonomous equipment in multiple off-highway applications, especially agriculture, mining and construction vehicles. Autonomous technology is now an essential element of the way off-highway manufacturers envision the future of equipment design and operation. Regardless of their level of autonomy, these vehicles will need to be outfitted with components that can meet the demanding environment of off-road conditions.
Incorporating these trends into the design of equipment presents multiple challenges to OEM manufacturers. In the absence of having an operator physically present, autonomous off-highway vehicles will benefit from being connected with IoT-type systems by also securing and sensing the status of physical doors, equipment access hatches and storage areas. At the other end of the spectrum, where operator presence is still required, machine cabs are evolving ergonomically with the need to support multiple operator screens and touchscreen interfaces, better seating and increased visibility.
Operator Ergonomics in Autonomous Vehicles
In some environments, such as mining or agriculture, the vehicle moves on a pre-determined path, which makes it a perfect fit for GPS-linked autonomous or assisted driving. Therefore, today’s off-highway equipment operator is much more than a driver, as they are often tasked with having to operate multiple types of equipment. During operation they must be able to gage the efficiency of the work being done, and provide service and maintenance as needed, all in addition to ensuring the safe operation of the equipment.
These operators are often required to spend long hours in their equipment. In response, OEMs are concentrating design efforts on enhancing the operator environment for comfort and convenience. This results in OEMs selecting hardware components that not only enhance functionality but also improve safety and the end-user experience.
For example, the number of screens has been increasing within the cab interior so that they can better monitor the status of a piece of equipment. These screens are the essential tools the operator uses to accomplish tasks and monitor the efficiency and operation of the system.
Off-highway vehicles (especially in construction) are often rented or shared by multiple operators on a crew. Just like seat and steering wheel adjustments, from an ergonomic standpoint, these screens also need screens positioned to account for the height differences of each operator.
The use of positioning technology that has intuitive touch point characteristics and response can be extremely useful in these applications. Design engineers can improve operator ergonomics and maximize usability by incorporating display mounting and hinging solutions with engineered positioning technology into cab designs.
For instance, there are hinges with integrated constant torque that allow single-handed adjustment of connected monitors and are engineered for the higher levels of vibration found in the rougher operating environments of off-highway applications. Constant torque hinges use engineered friction to provide a specific resistance against motion. Just like with laptop computer screens, they allow the positioning of a cab operator screen at any angle for tens of thousands of operating cycles, without any degradation of torque—even under high vibration conditions.
At the same time, repositioning is very easy: An equipment operator can move a screen to a better angle with one hand while continuing to safely drive the vehicle or operate equipment. To accommodate operator preference, it is essential that a display mount support the screen or monitor during vehicle operation, yet be easy to reposition through the full range of motion without having to secondarily turn set screws or knobs.
EAS Helps Improve Off-Highway Security & Operations
Extending the reach of the IoT to include mobile equipment is now well-accepted in a variety of industries, particularly in the logistics and delivery segments. Off-highway equipment fits cleanly into this same paradigm: These are industrial vehicles whose productivity, efficiency and safe operation need to be managed at both a site-by-site and enterprise-wide level.
To ensure the safe operation of any autonomous vehicle, there must be a sophisticated network of sensors that feed the vehicle intelligence—and capture and communicate that vehicle’s condition, location and operating status back to the owner or operator. This system-wide intelligence provides the OEM with the ability to enhance the security of off-highway equipment.
There are cloud-based technologies available that can provide a better and more simplified means of controlling and monitoring access to devices, systems and equipment.
Until recently, off-highway equipment security – including access to operator cabs, toolboxes and externally mounted equipment – was often very basic: a mechanical key was kept in a maintenance locker and tracked via paper records, for example. In this case, security from theft and vandalism is minimal as keys can be copied.
The introduction of electronic key fobs increased the level of security but still required a physical key be provided to operators, tracked and managed. Particularly in the construction equipment marketplace, this can be a time-consuming and complicated process.
Providing electronic access solutions (EAS) within the larger IoT digital landscape can elevate the intelligent access to and control of off-highway equipment. Integrating this technology into off-highway equipment involves adding electronic mechanisms that tie into the equipment controls in place of physical locks and keys. Just like a valet key provided for a car, electronic latching can be used to limit access, such as granting the operator access only to the cab and ignition, while allowing maintenance personnel full access to engine hoods and toolboxes.
Major component suppliers are now offering electronic access solutions that integrate BLUETOOTH® technology with electronic locks to simplify equipment access and key management by allowing an operator’s smart device—typically a smartphone—to act as a “key”. Time-based, virtual keys can be sent wirelessly to a smartphone application via a cloud-based web portal, simplifying the assignment of keys to multiple users and equipment. Operation is intuitive, as the operator or site manager simply opens the app to see their virtual keys, along with the associated locked equipment location, description and period of access time.
This can be particularly useful for the heavy-duty equipment rental market. Currently, rental equipment is stored in a dedicated location with an attendant required to handle the transaction and hand over mechanical keys. This can impact machine utilization and return on investment (ROI): If work on a site has to cease a half-hour before the end of a shift so that all the equipment can be returned to a secure location, productivity can suffer.
Electronic access solutions can eliminate this requirement as the rental agent can provide access remotely. Once the renter is provided access via the cloud, the renter need only approach the equipment and click the access button on their app, which transmits the encrypted BLUETOOTH® signal to the reader, unlocking the door and sending a record of the access via the smartphone app to the cloud. A further advantage of BLUETOOTH® technology is that it acts as a proximity device that controls access to locks and latches. Therefore, the user does not need to be connected to a wireless network to open the system, allowing for secure access to equipment even in remote locations.
In addition, this technology allows the equipment rental company to monitor access wirelessly and remotely from any Internet portal without having to connect to an existing security network. This technology is compatible with the IoT and can be used to track maintenance activity and anticipate future equipment repairs.
IoT Data Enhances Operations and Predictive Maintenance
One of the core advantages offered by implementing IoT architectures is the virtual flood of new information that intelligent sensors, controllers and other elements will provide. Operating data from EAS-equipped off-highway vehicles offers the same opportunity.
Agricultural and mining operations, construction firms and equipment rental companies will benefit by shifting from traditional methods used for gathering data, such as spreadsheets and manual data entry, to software or cloud-based analysis and monitoring.
One of the most important advantages is the real-time aspect of this information: Electronic access systems identify who is using what equipment and where it is in use, in real or near-real time. This data can then be integrated with other data streams within the equipment for more comprehensive equipment utilization information, aiding in equipment planning, cost analysis and distribution, and other management areas.
Properly maintaining heavy-duty equipment is a crucial management topic for owners and operators. The reliability and cost are main drivers in the ROI of their equipment, with higher efficiency continuing to be the primary goal. Today, many contractors choose to go to equipment rental providers rather than buying or leasing their own to save on costs associated with long-term maintenance and upkeep of heavy-duty equipment.
Because the renter doesn’t own the equipment, often the operator using it every day is not concerned with routine maintenance activities, such as changing an air filter or servicing the engine. However, IoT- enabled autonomous vehicles typically have multiple internal sensors gaging the “health” of the engine and auxiliary equipment. These sensors can now provide feedback for predictive maintenance, helping to avoid costly repairs and downtime.
Incorporating electronic access solutions into equipment that connect to these systems simplifies remote monitoring for the rental provider. To reduce the likelihood of equipment failure, off-highway equipment providers can use the data generated by autonomous systems to monitor the maintenance needs of a vehicle remotely, from anywhere in the world.
In addition, intelligent latches can control whether an individual can gain access into a maintenance area of the vehicle. The owner can also track door status of the equipment, when an access panel was opened, if it was closed, who accessed it and can even trigger alerts to the driver if a door is not properly secure. For each time the door is accessed, a digital record of activity is generated that can be used later to improve vehicle efficiency. This information is available remotely and can be networked with other security systems that connect with the IoT.
Elevating Off-Highway Equipment Value
Applying advanced technology to the challenges of operator ergonomics and equipment access can help off-highway equipment be better utilized, safer and more productive. The advent of assisted driving vehicles means design engineers should improve operator ergonomics and maximize usability by incorporating display mounting and hinging solutions with engineered positioning technology into cab interior designs.
EAS technology enhances operational safety and security by ensuring that only properly trained and authorized personnel have access to heavy-duty equipment. Like other IoT-enabled systems now being implemented in manufacturing and logistics operations, Electronic access systems in off-highway equipment can also be used to generate valuable information about equipment uptime and utilization, personnel efficiency and operating costs. As with other types of information generated by IoT technology, it is ultimately up to the equipment owner or operator to intelligently mine and analyze this data and apply it to their operational challenges.