Ensuring Passenger Comfort in Aerospace Seating Design
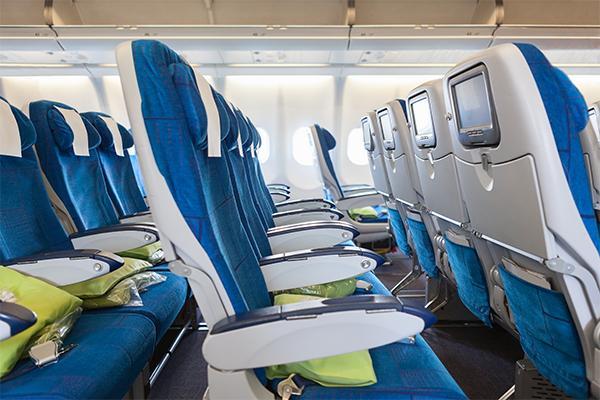
There is considerable discussion in the media across much of Europe about the intention of governments and rail partnerships to seek to compete more effectively with short-haul flights by improving the infrastructure and service of Europe’s high-speed rail network.
Cost and time remain key drivers when choosing a preferred mode of travel. However, as airlines promote the highest levels of passenger comfort through ergonomically designed cabin layouts, expectations of a more sophisticated travel experience are equally manifesting themselves in the minds of rail passengers. So with the high-speed rail network forecast to continue growing steadily over years and years to come, will rail seating stand up to comparison with the Aerospace industry seating benchmark?
Compared with aircraft, and with a similar drive to reduce weight and power consumption, the rail seat is typically larger and boasts more space and legroom: yet it is the passenger’s complete on board comfort zone which is under scrutiny when it comes to defining value for the passenger in terms of comfort and functionality.
What is the on board comfort zone?
The on board comfort zone is that area of space on a train (or an aircraft) which passengers can call their own, in return for the purchase of a travel ticket. It will mean different things to different people, and may have various features depending on which section of the plane or train the passenger is in.
However, every seat, regardless of class and ticket price, will have “touch points” which impact the passenger’s perception of comfort and functionality. These “touch points” relate to elements such as headrests and armrests, drop-down tray tables, tilting screens and tablet holders, whose functionality can be optimized through sophisticated positioning hinge technology to deliver an enhanced passenger experience.
Positioning hinge technology created by Southco is now proven in the Aerospace and Automotive industries, where developments have been driven by the key design consideration of providing ultimate comfort and easy operation for the end user at every possible “touch point”.
Improving the passenger experience
So how can this proven hinge technology be adapted for rail to deliver that all-important first impression of customer comfort and convenience?
There is an increasing expectation for infotainment screens that are incorporated into passenger seating. These screens can be adjusted to the optimum viewing angle using a simple positioning hinge with integrated friction technology.
For economy seats without such screens, presumably for reasons of cost as well as for fear of vandalism, a tilting shelf with similar integrated positioning technology that allows the passenger to fine-tune the viewing angle of their own tablet or smartphone is an attractive option.
A positioning technology hinge allows for infinite adjustment increments and resists movement due to vibration, train acceleration and braking or gravity. The latest technologies eliminate the variation and quality issues associated with spring washer solutions, creating maintenance-free, highly reliable and consistent screen adjustment.
Most economy carriages currently have tables which fall into the space above the passenger’s lap. Adding a friction hinge provides a simple means to enhance the passenger experience by allowing the table to be positioned according to the preferences of the passenger, but preventing the table from descending in an uncontrolled manner once it has been adjusted into place.
Meanwhile, armrest joint mechanisms can also benefit from reliable constant torque technology. Asymmetric torque allows the armrest to be lifted with little effort by the passenger, it but contains enough resistance to stop it from falling or dropping unexpectedly.
Headrest functionality can also be enhanced by the use of these positioning mechanisms to provide customized support, improving comfort and reducing travel fatigue. The unique advantage of asymmetric torque is that the headrest can be easily pulled towards the passenger but resists the weight of the passenger’s head leaning against it.
Adjustable headrests are now considered standard issue on aircraft, in every class of seat. This is certainly not generally the case for the rail seat, where a majority of headrests have not been designed with passenger comfort in mind.
How is reliable positioning achieved?
Southco’s friction technology draws on many years of research and development, combining superior materials and manufacturing methods to produce optimum quality technology at an acceptable price point.
The most commonly used alternatives for providing positioning in rail interior applications include devices based around spring washers, which are clamped using a threaded tension bar or bolt. While representing a low-cost solution, these devices typically have the disadvantage of high variation and inconsistency, as well as a relatively low cycle life before a repair or adjustment is required. This means the total cost over the life of the application could be excessive, and certainly the chances of a passenger noticing the poor quality is increased.
Friction technology, however, is straightforward: finely-tuned torque elements are mounted to the hinge axis to provide repeatable asymmetric torque. The design effectively removes internal clearances within the hinge such that there is no play or backlash introduced into the joint.
Part of the know-how involves balancing the static and dynamic frictions of the hinge joint. Too much static friction and the result is a “stick-slip effect” resulting in a very unsatisfying jerky motion - too much dynamic friction and the wear rate of the mating surfaces increases significantly. For the hinge to move smoothly, repeatedly and with constant resistance and minimum wear rate, the relationship between the surfaces must be in harmony.
The asymmetric torque gives the advantage of resistance to the object when descending but less resistance to the lifting effort. This is achieved as the torque element works like a spring, opening slightly when rotation occurs in one direction to lower the torque, and clamping down tightly on the shaft when rotating in the opposite direction to maximize the resistance. This relationship is not significantly affected by changes in temperature, which can be a problem with viscous fluid dampening devices.
Simply varying the quantity and orientation of these elements enables the creation of hinges and systems perfectly matched to the weight and feel for each application, with the torque and ‘feel’ remaining consistent and smooth across an extremely high number of cycles. Southco systems are preset at the manufacturing facility, with no requirement for adjustment by the installer or end user. The diameter and axial length can also be configured to package the maximum torque in the smallest available space.
When the seat reaches its end of life or a predetermined refurbishment period is over, then, if necessary, the hinge can be replaced without any specialist expertise, safe in the knowledge that the joint will again outlast the next set of upholstery. This compares favorably with the more frequent overhaul typically required to refurbish seats.
This technology is at the heart of a number of Southco’s off-the-shelf solutions for mounting into most plastics, composites and metal structures. A range of products is now available to suit torque requirements for applications as small as a flip cover on a mobile phone sized device, right up to supporting panels or equipment weighing 15kg or more. Torques can range from fractions of Newton-centimeters to 10s of Newton meters. The upper boundary is only restricted by package constraints and by the limits on the user forces customers are likely to apply. Very heavy loads can be supported using added counterbalance features that work in combination with the friction technology.
This technology can be over molded into plastic or composite structures or integrated into custom housing designs and configurations to suit the application. It can even be combined with dampening, detent and counterbalance features to exactly match the functionality desired by the designer and the end user.
These innovative technologies are now all available as standard solutions to the rail industry to allow the on board comfort zone to compete with that of airlines and other forms of transportation, and promote the highest levels of passenger comfort from economy class right up to Business/ First Class. Friction-based solutions can improve the feel and perception of quality for headrests, armrests, tables and infotainment devices - in fact, for every major element of the on board comfort zone that the passenger will interact with while on the train.
Use of these solutions will enable rail operators to promote highly ergonomic passenger comfort zones, thereby meeting the expectations of the more sophisticated travel experience expected by the modern rail passenger.