Designing Enterprise Server Hardware to Protect the Physical Side of the Internet
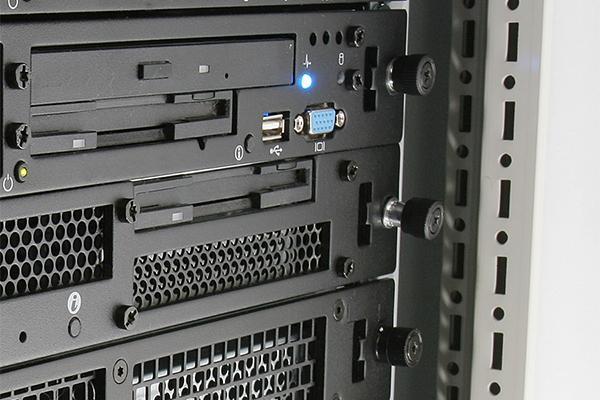
As the demand for data capacity continues to increase, massive investments are being made to engineer and protect server technologies, communications systems and data center enterprise equipment – the physical components that make up the Internet, and store critical data.
But every server blade containing valuable data needs to be secured into a server rack, and the technology for securely mounting and latching sensitive electronic components into the enclosure is just as critical as mounting components to the mid-plane/back-plane or securing PC board components to a sheet-metal sub-pan.
Over the past several years, various open sourcing models and globalization have changed the way that technology companies approach data center designs, from servers to networking and storage. But with many more options now available via globalization, not all hardware is created equal. How can engineers be assured their chosen enterprise latching and fastening solutions meet the quality levels necessary to keep data safe and secure?
Avoid Adding Service Costs
Today, different open sourcing designs are being offered at lower costs than traditional enterprise servers. However, open sourcing engineering projects presents new challenges for the designers tasked with integrating these solutions, which sometimes leads to inferior products being used.
Physical fastening hardware products are now widely available at an upfront lower cost through contract manufactures – typically by unknown suppliers. These products may not meet the same level of quality standards required to perform in all critical environments – which can ultimately lead to additional service costs, lost engineering time to redesign systems, and ultimately down time.
Increased data capacity has amplified the cost of line cards by tens of thousands of dollars, making quality latching and fastening hardware paramount in the server design process. Integrating captive screws and inject/eject solutions designed with quality materials and proven engineering from the beginning can mean the difference between redundancy and downtime.
Considerations for Inject/Eject Hardware
With any inject/eject mechanism, there is always the potential risk of damaging connectors, breaking latches or faulty switch engagement when inserting line cards to the chassis – all due to increased forces needed to seat the connectors. For instance, if the connectors are not seated correctly during insertion the module may lead to data disruption or an intermittent signal.
Hot swappable systems are crucial in managing the safety of stored data, because if one system is down and running without a backup; the data is at risk until maintenance can restore redundancy. Integrating a hot swap switch directly into the ejector is an efficient means to assure the hot swap timing is correct. When the ejector lever is released and signal is sent by the integral micro-switch, it in turn releases that data successfully to a redundant line card, so the faulty card can be serviced or swapped out.
Enterprise hardware products should be engineered with quality materials and minimized design footprint, to accommodate multiple faceplate thicknesses and microswitch styles.
Another key factor in the design of mechanical lever ejectors is material selection. Inferior metals affect aesthetics, where inferior finishes or corrosion can impact the intended finish of the part by the industrial design team. If the right finish or non-qualified finish supplier is used to save on budget, it can cause quality issues after multimillion dollar units have shipped, leading to disruptions and lost revenue. Risk is also present when inserting a line card to the backplane. Ejector systems provide the correct amount of “wipe” by ensuring that board connectors interface properly with the backplane of the shelf.
For instance, there is a minimum amount of travel required to maintain the signal integrity through the mating connector. If that travel is not achieved, there is an intermittent signal, or through vibration that signal could be lost. Tolerance stack ups within the system may also affect wipe. These design parameters must be taken into consideration early on in the design process. Working with a supplier that can run mold flow analysis, DFM and DMFEA simulations saves time and potential quality issues once products are released.
Considerations for Captive Hardware
Material selection is equally important when specifying captive hardware, which secures different components, or PC boards and mother-boards securely in place. With captive screws, there are a wide range of materials to choose from, but using the most economic option upfront can lead to operation issues down the line.
Finishes may not withstand fluctuations in temperature and colors may fade over time. Using high grade similar materials can also lead to galling. In many cases, the metal flakes generated by stripping the thread fall onto the PC board and cause components to short, once again leading to lost data or data disruption. Stripped hardware also prevents technicians from accessing the server card, further contributing to added costs.
Material and finish selection also impacts hardware strength. If not plated properly, the metal used in the screw design can retain absorbed hydrogen (hydrogen embrittlement), which can affect a screw’s ability to withstand applied forces. A qualified supplier will perform such tests as hydrogen embrittlement after the plating process, which can prevent issues when forces are applied in the field.
Southco’s SMT 4C Captive Screws feature heat-resistant prism knobs that withstand high temperatures during the reflow process and provide color matching capabilities with multiple tool recesses available.
The installation process can also contribute to added service costs. During PC board assembly, stress created by pressing captive hardware through pre-drilled holes can cause cracking or damaging the layers of the PC board, resulting in added scrap costs. Different installation processes are now available, such as Surface Mount Technology (SMT), which enables captive screws to be attached to the PC board during the reflow soldering process at the same time as other surface mounted components, resulting in lower overall installation cost.
Choosing a Proven Supplier
Open sourcing models offer unlimited options for new lower cost suppliers; however, choosing inject/eject mechanisms and captive hardware from a proven supplier can save time and additional engineering resources from the start of the project. Proven engineering expertise can help address potential risks early in the design and development, preventing the risk of downtime and added service costs.
Integrating a validated solution at the beginning of the design through a proven supplier that offers DFM or DFEA analysis is more beneficial over time, because it reduces the likelihood that additional engineering resources are needed due to component failure in the future. As a result, engineers can spend more time dedicated to their equipment and launching the project on-time.
When choosing enterprise hardware products, engineers should also examine a supplier’s manufacturing processes, including die-casting capabilities and in house powder coating, as well as how the supplier manages their supply chain. Additionally, enterprise hardware products must be compliant with global industry standards, such as ROHS or other directives, regardless of where they are manufactured.
Choosing a supplier with a global footprint allows manufacturers to secure resources wherever they are building equipment in the world – allowing an application to be designed in one country and manufactured in another, and facilitating the sourcing of replacement components where they are needed.
Conclusion
Latches and fastening products engineered at a lower cost may not always meet the same level of quality as solutions acquired from a proven supplier. The same investments made to protect valuable data stored in the data center from virtual threats should also be applied at the physical level, which includes the racks and switches that house and transmit the data. By specifying enterprise hardware engineered with quality materials, engineers can prevent service issues and downtime, while keeping data safe and secure.