5 Questions to Ask When Choosing a Stainless Steel Hinge
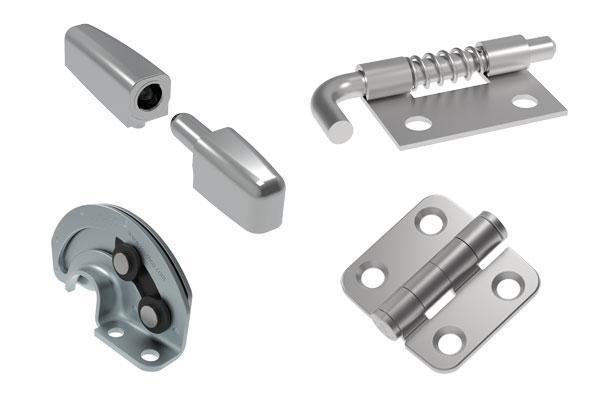
Good design frequently goes unnoticed. This is because, firstly, a well-functioning product naturally receives less recognition than a product with flawed operation and, secondly, the design details that constitute a high-quality product are often not obvious to an end user.
This observation is certainly true for many hardware components: while playing a key role in ensuring consistent performance of an overall product solution, often not much attention is given to the specification of such elements. As a result, the inferior performance of the product due to specifying hardware components that are not the most appropriate fit for the application may only come to the forefront when the product has already been launched.
Using the example of stainless steel hinges, which are used across many industrial applications and are readily available in the market, asking the following questions will help differentiate between the many available hinge suppliers to select the product that is right for the application at hand.
What do the testing and manufacturing processes reveal about potential performance?
For many engineers, cost and convenience play key roles in the decision-making process, but they are only one element of the overall design process. Short and long-term performance are also important, but it can be challenging to assess when comparing one solution to another.
One way to do this is to evaluate the manufacturing and testing processes involved in developing the hinge, by asking a potential supplier how they test for and assure quality, durability and performance. Do they have any proprietary processes in place to ensure that design and aesthetic impact are matched by a high level of functionality? A proven supplier should have manufacturing, testing and assembly processes in place that provide a high level of product integrity -– even in the most demanding application environments.
Does the product actively help with meeting regulatory standards?
In many cases, compliance is not often the first thing that comes to mind when thinking about stainless steel hinges. However, choosing the right hinge can help meet the demands of industry-specific regulations. This goes even further than having the correct material grade to meet specific industry standards.
For example, asking whether the hinge has been tested for performance against moisture and dust (NEMA 4 / IP65) or against shock and vibration (EN61373). Even a small detail such as an exposed opening for a screw fitting has the potential to make controlled environments, such as food or pharmaceutical applications, more vulnerable to contaminants. Hinges that are constructed with stainless steel offer a high level of corrosion resistance and can withstand harsh cleaning agents and exposure to contamination.
A hinge with exposed openings or sharp corners can also increase the risk of injury and accident in environments that are constantly in motion, such as ambulance interiors. In this case, stainless steel hinges with optional covers can help prevent exposure to injury by shielding sharp edges and providing a smooth, seamless surface.
Does the product provide consistent aesthetic impact?
Every surface mount hinge should look fresh and new when it has been delivered from the manufacturing facility, but what about two, five or even ten years down the line? Also, while it is relatively simple to maintain uniformly consistent hand-polished hinges in the hundreds, will the standard still be the same when the parts are purchased by the thousands? To avoid these pitfalls, engineers should check that the hinge is processed in a way that ensures it has an identically high-quality finish every time, no matter how large the volumes.
Proven suppliers will share the processes they use to provide long-lasting corrosion resistance, durability and “cleanability”, and how they assure a refined look without sacrificing functionality. When choosing a supplier, consider whether they offer optional features which enhance the appearance of the hinges without impacting their function, such as a high gloss finish option and cover options to hide mounting hardware.
What other benefits does this product bring to the application?
Asking the right questions early on in the design process can potentially highlight where product choice can bring added value to projects in markets such as industrial machinery, HVAC and electrical equipment. A stainless steel hinge should have a consistent, reliable performance over its life cycle and this is where value is created, as no ongoing investment or maintenance is required.
Watch out for the risks of selecting a surface mount hinge that is only available as a standalone part. Stainless steel hinges that are instead created as an entire system with a range of hinge leaf configurations and sizes, and optional complementary parts provide more design options and guarantee that all components will work together. Furthermore, there may be the requirement for locks or latches on the same application where the hinges are used.; Selecting all necessary components from one supplier versus many ensures compatibility of solutions and offers more design flexibility.
Will the part provide Return On Investment for the life of the project?
Cost is often a major aspect of the component selection process. But it pays to go further by assessing the Return On Investment of a hinge over the entire life cycle of a project. Look for options that are competitively priced, but also provide further advantages, such as whether the hinge you’re considering has the potential to help resolve a design or function problem rather than performing one basic role.
Does the hinge assure high corrosion resistance for long-term performance or offer additional optional features that improve the quality of the end product or user environment? Asking a supplier how their stainless steel hinges are manufactured can potentially enhance the Return On Investment of your entire project.